Note the title is "A Journey Towards", coming closer and closer to attaining it, but knowing that it isn't possible.
Ok, after seeing the flame job that The Wood Whisperer's, (Marc Spagnuolo's) review of the Incra fence system wrought "I swore I would never.....blah, blah, blah, blah, blah." Yeah, didn't take me too long to get over that. I have to be smarter than this. Ok, I am; but I am also one to point out flaws where I see them too. Well, maybe not flaws, but definite room for some thought out improvement. People may think I am anal retentive, OCD, ADD, Asperger's inflicted, or someone who just likes to picks apart every ridiculous thing with little comprehension of reading the instructions first. Well to them I say, "I do to read the directions first! Very nice pictures."
That being stated, I must also fill in a little background. I am one of the insane type who actually likes to sharpen tools. There is something "meditational" and Zen-like about the path to having two shiny mirrored surfaces merging to a straight or curved line in a precise flat plane. It is beautifully mathematical too. Then there is the great pleasure in taking the sleekly made razor and sliding it through wood fibers, neatly shaving or chopping them to desire without deforming their neighbors.
If you want to blow off the my personal history of sharpening click here. But I'll be hurt and you'll be cursed with 7 years of rusty tools.
I started off using oil stones; when I was first learning the difference between a chisel and a screw driver with a sharp edge. Why, you might ask? So did I. It was what my father used on his pocket knife; and I, for another brief moment in time, was an idiot. I tried sharpening chisels and jointer blades with them, both with too much work and not enough quality results. Oil stones suck. NEXT!
After that I started looking around, unfortunately it was at the "big box stores". I figured that I would have to have a grinder to make hollow bevels, right? So I went out with little money, and littler sense, and picked up a Delta high speed grinder with no speed control. I even went so far as to buy the softer, finer grit stones to grind without glazing and trashing the tool in the process. Strike two, ok maybe still strike one; it does still come in handy as a buffing wheel, but with a stone in place it really shouldn't be used on a chisel or any other blade without a fire extinguisher and a bucket of water handy. NEXT!!!
My third venture was the Delta Sharpening Center 23-710 with the 23-715 extra long planer blade holder, things were starting to look really good. It has a 120 grit dry wheel which spins at about 3,600 rpm (still not a good speed), and a wet 1,000 grit wheel that spins at 400 rpm. This one was very nice, but the quality control on it was a little sub-par. Really I have only three issues with it.
- First, the tool rest alignment design doesn't allow for slight adjustments the angle of the plan that the tool sits on. Mine was off, or not co-planar, with the large 1,000 grit wheel to the tune of about 5 - 8 degrees. This made my tool rest very "askew" and so my edges.
- Second problem was that I still wasn't able to do gouges very well without causing hideous grooves in the soft 1K grit wheel; which I would have to then flatten out, wasting a large portion of the stone.
- Third, the dry wheel spins far too fast and would still burn edges if I wasn't closely watching. Really not that big of a deal, but the real issue with the 120 grit dry wheel was that it is hollow in the center. It is bowl shaped. If you don't monitor the thickness of the wheel from the inside bowl to the outside edge there is going to come a point where centrifugal forces are going to cause it to fly apart and put out an eye.
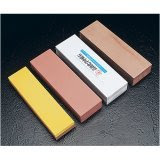
There are some real down sides to water stones I will admit:
- They can be expensive, very expensive in the higher grits. A 15K stone can have a price tag in the hundreds of dollars.
- They can be messy. They are generally soaked and then at least sprayed frequently with water to help remove the used abrasive and metal.
- They can be a royal pain in the ass to keep flattened. A good machined granite slab with sand paper can flatten all but the coarsest 220 grit bricks. For that type you need a special flattening stone of silicon carbide for that beast.
- Irregularly shaped chisels and gouges (especially of the turning variety with their long handles) can be very awkward to do and they generally produce nasty grooved that must be reflattened, unless of course you spend more mullah on stones made for each shape.
- They can be messy (I think I got that one), 6), 7), etc.....add some stuff I am sure you have your own list but that is my 5.
But even with these issues they have equal benefits to counter balance, respectively:
- A good balanced set, used properly, can last you many many years.
- The "messy" water traps 100% of the metal "filings" or dust and contains it for controlled disposal, also you are ensured that you have a clean fresh path for the best sharpening.
- Ok, they can still be a royal pain in the ass to keep flattened. But it isn't that bad, especially if you have a granite slab and good sand paper.
- Once flattened they are superb at truing, honing, and putting the brightest mirrored surface on any regular chisel, plane iron, planer or jointer blade.
- Ok, it is messy but with each pass you get a good clean set of abrasive material to bring out that dazzling shine and better-than-razor sharp edge, and you don't have to keep a piece of rubber handy to clean it like sand paper. Not to mention that you also are generally going to have the mess contained in a water bath.
Fourth and a half, I have tried sand paper on my granite slab. And it does work great, for truing and tuning planes. The three biggest issues I have with sand paper is; that once you start getting into the finer grits (anything below 320) the metal starts to cake up after just a few passed. You then have to brush, rub, scrap, and knock off the metal "crusties". Now, while yes you can use water at that point to try and lift and remove the metal dust, it is still a mess and you have to constantly reach for the spray bottle. If you keep the coarser grits dry to ease the mess you still have a lot of nasty metal dust. And the last is that you have to special order grits higher then 1500 to 2000, and even grits past 600 you can usually only get at decent auto parts stores. Oh, and they rip. And, oh, oh, and they have a relatively short shelve life. Generally it is recommended that you toss the paper backed sand paper after about 6-12 months, used or not.
Now the last one. I know; you have been patient and hopefully this won't be a total wet blanket.
The WorkSharp 3000. TaDaaaa!!!!!
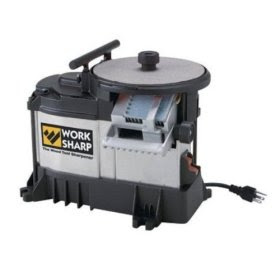
I have run this through a long several nights of tests, not weeks or months, with most of my chisels, blades, gouges, and others; all except for my jointer and planer blades. The jointer blades I am sure I wouldn't be able to do with this system because they are just too long, a little over 8". Same issue with the planer, but the planer's blades are more the disposable type. For both of these it is going to be sand paper, water stones, or most likely the Delta Sharpening Center. After all, I did buy the extra long holder, and with proper flattening and patience it does the best job, at least down to 1,000 grit.
I have studied it, I have tried to analyze it with my usual needs from a sharpening system. I turn, I chisel, I do some carving, and I love me a good sharply tuned hand plane, and I think that this report will cover all the bases I need to cover. If not, I am sure someone will let me know. I have shared these with Marc Spagnuolo and hopefully he'll see fit to edit them up and share with others on his site. (Like Marc, I am only Joe Blow and not a paid technical reviewer with weeks to dedicate to "testing" stuff, which is a loose term in itself. If you don't like what you read, suck it up, spend your own $200, and write your own.) Here is the self-edited version of what I found:
- The sand paper clogs too quickly, even on the coarser grits (the grits with the lowest numbers). They have to be cleaned constantly with the supplied rubber block cleaner to be effective. Also you have the ability to sharpen under the disc with a 5 degree incremented tool rest. In order to properly clean the under side of the disc you have to take the disc off, real pain.
- Speaking of taking the disc off. When you apply pressure to the disc, and the disc is spinning, it causes the hold down bolt to tighten. You would be surprised how a little drag on the outside of a 6" disc can transfer to a LOT of torque on a center bolt. I wore my hand red several times getting the bolt loose. Maybe a bigger handle on the retaining bolet would help a lot.
- The coarsest grit that is provided isn't coarse enough for moderate metal removal. It is great for light metal removal, honing, and finishing to a near mirrored surface; but if you are looking to flatten the back of a wide blade that is fresh out of the box, or damaged, you will need to buy a coarser grit (like a 100 grit paper) to start with.
- The sticky backed sand paper is prone to air bubbles which is a leading cause of sand paper blow out. This at least can be corrected by using a needle to open a passage for the air to escape through the paper. This is a huge issue especially for the finer grits.
- The only positive angle stops are at 20, 25, 30, and 35. This is good for basic sharpening, but you are unable to get that 1 to 2 degree micro-bevel that I have been spoiled into getting with other devices. You can get a very decent 5 degree micro-bevel on the first three angles by setting it up a 5 degree notch though.
- The ring that surrounds the spinning disc is made out of aluminum. This means that it is not conductive to magnets. It would be of great help to be about to attach magnets to the ring to attract some of the metal dust that is flung off the disc.
- The metal dust is an issue. With the WS3000 it is flung everywhere. One of the best and worst things about water stones is the water/slurry that is made during the sharpening process traps the metal "filings" or dust that is made, bonus for them; but the negative side of the coin is that it is sloppy and a wet mess afterwards.
- With the top rest that can be used, that can also be mounted under the disc, for free hand sharpening there is no angle indicator. Ok, I hear the "but that is what free hand sharpening is all about." Well that is fine, but there are many times during my sharpening experience that the iron (that is what the blade of a plane is called) is pulled or jerked to the side. This throws off consistent sharpening. It would be good if they provided at least a registration plate to slide on to the tool rest, like a wide tight fitting washer that could be used to make sure the blade was perpendicular to the disc while sharpening, if it was desired.
- Another slight issue is that unless you are going free hand you are limited to a 2" blade. That means that any plane blades over that and you are hosed, this includes #4 1/2, #5 1/2, and up. But look toward the bottom for a trick to over come this short coming.
- You can basically use any 6" PSA disc (PSA is the sticky backed type) on the system. As long as, of course, you punch a 3/4" hole in the dead center. And you can get those at any hardware store, but it is generally not possible to find the higher 1000+ grit variety. So for those you are going to have to go to WorkSharp; or MAYBE a higher end auto parts/painting place or the Internet or maybe make your own. A great thing because, again, you can get 100 grit discs for the more hard core metal removal if you really toast a blade.
- Another one for the plus side is that sharpening gouges is great. The view-thru wheel is wonderful for irregular shaped blades that you need to watch as you grind. Although you still need to deal with the free handed idea that you can't set a stable angle without some practice, the tool rest can be mounted on the bottom to help with any blade. This is where this system shines. With stones and every other sharpening system I have used, outside of MDF and a molded contour with embedded diamond paste, this is the only system that truly allows you to effectively manage the shape and angle of the edge. By being able to actually look through the wheel you are able to hone an edge without wondering if I am bluing the edge or grinding it past the point of effectiveness.
- The aluminum flat tool rest for chisels and smaller plane irons acts as a decent heat sync to try and circumvent overheating. Trick Notice (click image right to enlarge, sharpening disc removed for clarity): The registration guide can also be moved further to the left than documented it expose a "corrugated" edge on the left. This does make it possible to sharpen blades a little beyond the 2" limit with proper registration; but since the blade is off the aluminum heat sync backing, you must be careful not to blue the edge.
I wouldn't toss my 120 grit small grinding stone on my Delta sharpener, it is great for hollowed bevels. I wouldn't toss my stones either, they are outstanding with my Veritas MK II guide for accurate angles and micro-bevels of 1 and 2 degrees. And I'll even keep the Delta high speed grinder, just using the felt buffing wheel, maybe even the softer bounded aluminum oxide wheels.
LQQK